En el vertiginoso campo de la fabricación de los dispositivos tecnológicos del mundo, Pegatron Corp. inicialmente aprovechó la IA para obtener una ventaja. Ahora, está a punto de crear digital twins para optimizar aún más su eficiencia.
Más allá de que conozcan el nombre, la mayoría de las personas probablemente utilizó teléfonos inteligentes, tabletas, routers Wi-Fi u otros productos que Pegatron, con sede en Taiwán, fabrica en casi una docena de fábricas de siete países. El año pasado, fabricó más de 10 millones de notebooks.
Andrew Hsiao, vicepresidente asociado de la división de I+D de Software de Pegatron, está liderando el movimiento de la compañía hacia el machine learning y la Internet 3D conocida como el metaverso.
Desarrollar una Plataforma de IA
«Hemos estado recopilando datos de fábricas desde 2012 para encontrar patrones y conocimientos que mejoren las operaciones», dijo Hsiao, un veterano gerente de tecnología que ha estado con la compañía durante 14 años, desde que salió de ASUS, uno de los fabricantes de PC más grandes del mundo.
En 2016, el COO de Pegatron, Denese Yao, lanzó una fuerza de trabajo para aplicar una nueva tecnología que mejora las operaciones. El equipo de expertos en inteligencia artificial de Hsiao colaboró con los trabajadores de la fábrica para encontrar casos de uso para la IA. Uno de sus primeros proyectos piloto utilizó deep learning para detectar anomalías en productos a medida que bajaban de la línea.
Obtuvo resultados sólidos utilizando versiones modificadas de modelos de redes neuronales como ResNet, por lo que aceleraron el proceso.
Hoy en día, Pegatron utiliza Cambrian, una plataforma de IA que construyó para la inspección automatizada, la cual se implementó en la mayoría de sus fábricas. Mantiene cientos de modelos de IA, entrenados y ejecutándose en producción con las GPU de NVIDIA.
Menos Defectos, Más Consistencia
La nueva plataforma detecta hasta un 60% más de defectos con un 30% menos de variaciones que los inspectores humanos, y los empleados de la fábrica lo aprecian.
«La inspección manual es un trabajo aburrido y repetitivo, por lo que no sorprende que a los empleados no les guste», dijo. «Ahora, vemos a los empleados motivados para aprender sobre la nueva tecnología, por lo que permite a las personas hacer un trabajo más valioso».
El sistema también puede mejorar el rendimiento a medida que las fábricas ajustan los flujos de trabajo en estaciones de ensamblaje y embalaje para tener en cuenta las líneas de inspección más rápidas.
Los Modelos se Implementan 50 Veces Más Rápido
El sistema de Pegatron utiliza las GPU NVIDIA A100 Tensor Core para implementar modelos de IA hasta 50 veces más rápido que cuando los entrenó en workstations, lo que reduce las semanas de trabajo a unas pocas horas.
«Con nuestra plataforma unificada basada en DGX, tenemos nuestro lago de datos, conjuntos de datos y entrenamiento todo en un solo lugar, por lo que podemos implementar un modelo en un solo clic», dijo Hsiao.
Gracias a la capacidad de GPU de Múltiples Instancias en las GPU A100, Pegatron redujo el tiempo de espera de los desarrolladores para acceder a un acelerador de casi una hora a 30 segundos. «Eso nos permite programar dinámicamente trabajos como la inferencia de IA y el entrenamiento ligero de modelos», dijo.
Como parte de su trabajo de inferencia de IA, el sistema analiza más de 10 millones de imágenes al día utilizando NVIDIA A40 y otras GPU.
Triton y NGC Simplifican los Trabajos de IA
Pegatron utiliza el Servidor de Inferencia NVIDIA Triton, un software de código abierto que ayuda a implementar, ejecutar y escalar modelos de IA en todos los tipos de procesadores y frameworks. Funciona de la mano con NVIDIA TensorRT, un software que simplifica las redes neuronales para reducir la latencia.
«Triton y TensorRT facilitan el servicio a múltiples clientes y la conversión de trabajos a los niveles de precisión más rentables», dijo.
El equipo de Hsiao optimiza los modelos de IA previamente entrenados que descarga en contenedores Kubernetes integrados desde el centro NVIDIA NGC para el software optimizado por GPU.
«NGC es muy útil porque obtenemos con un solo clic los frameworks de deep learning y todos los otros componentes de software que necesitamos, cosas que antes nos tomaba mucho tiempo reunir», dijo.
Siguiente Paso: Digital Twins
Para dar otro paso en la manufactura más inteligente, Pegatron implementa un piloto de NVIDIA Omniverse, una plataforma para desarrollar digital twins
Hasta ahora, tiene dos casos de uso. Primero, probar Omniverse Replicator para generar datos sintéticos de cómo podrían verse los productos que bajan de la línea de inspección con diferentes orientaciones o condiciones de iluminación. Esta información hará que sus modelos de percepción sean más inteligentes.
En segundo lugar, está creando digital twins de máquinas de inspección. Esto les permite a los trabajadores remotos administrarlos de forma remota, obtener una mejor información sobre el mantenimiento predictivo y simular actualizaciones de software antes de implementarlas en una máquina física.
«Hoy en día, cuando un sistema queda inactivo, solo podemos revisar registros que podrían estar incompletos, pero con Omniverse, podemos reproducir lo que sucedió para comprender cómo corregir el problema o ejecutar simulaciones para predecir cómo se comportará en el futuro», dijo.
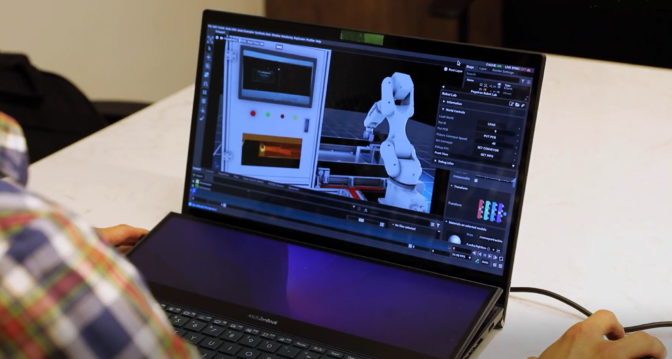
Además, los ingenieros industriales que se preocupan por el rendimiento, los ingenieros de automatización responsables del tiempo de inactividad y los ingenieros de equipos que manejan el mantenimiento pueden trabajar juntos en el mismo sistema virtual al mismo tiempo, incluso cuando inician sesión desde diferentes países.
Visión de una Fábrica Virtual
Si todo sale bien, Pegatron podría tener Omniverse disponible en sus máquinas de inspección antes de fin de año.
Mientras tanto, Hsiao está buscando socios que puedan ayudar a desarrollar versiones virtuales de una línea de producción completa en Omniverse. A largo plazo, su visión es crear un digital twin de toda una fábrica.
«En mi opinión, el mayor impacto vendrá del desarrollo de una fábrica virtual completa para que podamos probar cosas como nuevas formas de dirigir los productos a través de la planta», dijo. «Cuando lo creas sin una simulación primero, tus errores son muy costosos».